

The sturdy design of the oven ensures that it can fit securely into a larger operation, too. It's easy to add this machine to your collection of soldering devices, which can enhance your SMT production capabilities considerably. The height of the T8L table is adjustable, which simplifies the process of building a production line. Heating and cooling times are optimized to ensure that PCBs benefit from industry-leading soldering techniques. The oven contains 8 heating zones, which provide precise temperatures at different stages of the soldering process.
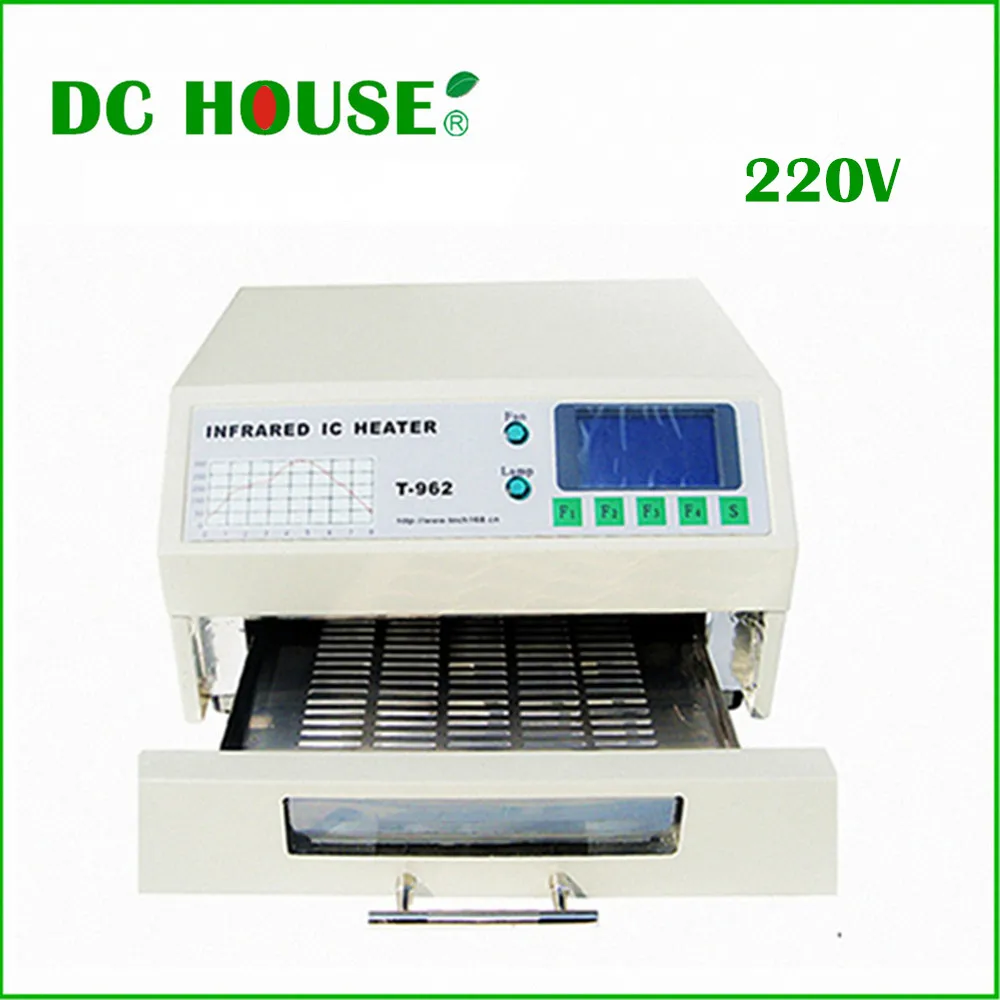
The T8L oven is an advanced soldering machine designed for the PCB manufacturing industry. Contact ZenTech today for more information on what modernized American manufacturing can do for your products.This item is available via special order only. Is your manufacture using the most up-to-date SMT production techniques? If not, it might be time for a change. Precision computer-controlled reflow ovens guarantee superior final products, again and again. The result of all this is a finished SMT circuit board which is smaller, more efficient, and more resistant to vibrations than older through-hole circuit boards. In some cases, special solvents may be used. So, the final step is washing the finished circuit, usually with simple deionized water and a mild detergent followed by air-drying. Most forms of solder paste leave a chemical residue, even those considered "no clean." Additionally, microscopic grit could have made its way onto the board during the manufacturing process.
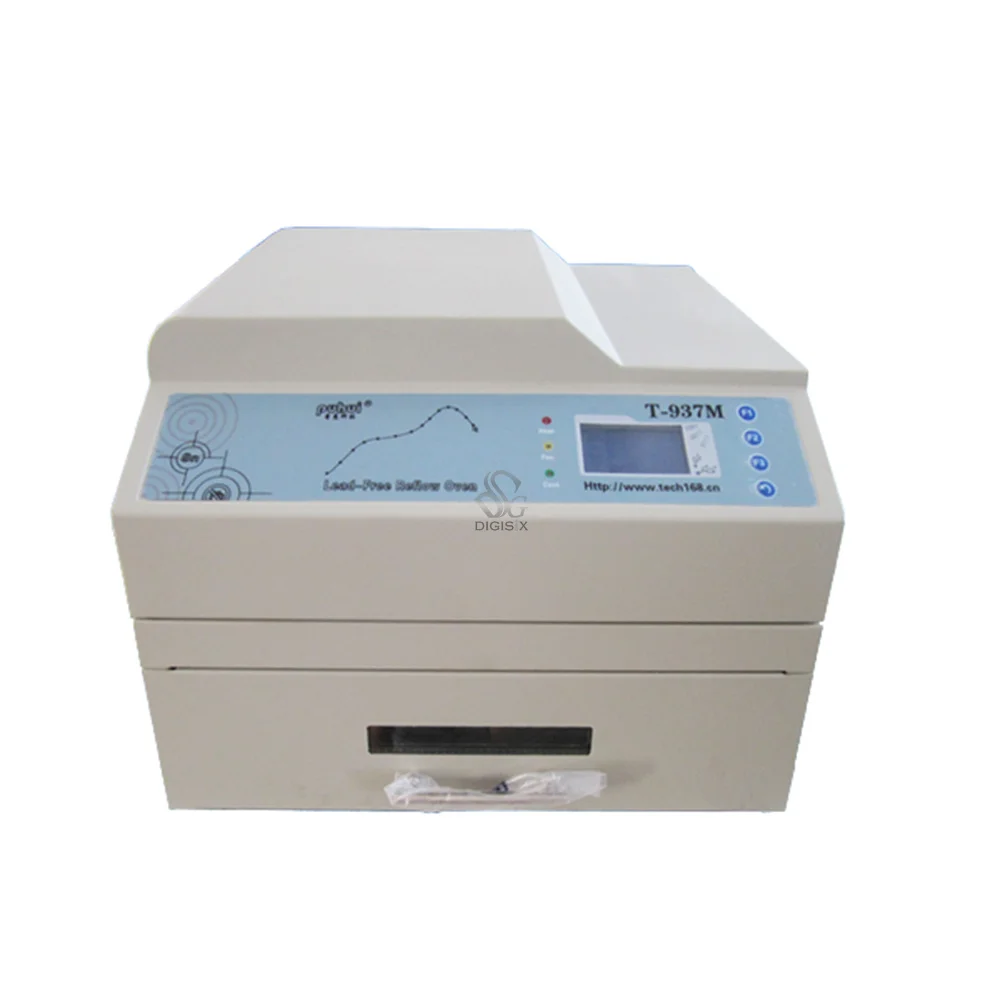
Not all manufacturing centers include a washing process, but they should - it's now commonly accepted by standards agencies such as the IPC. The cooling is more rapid than the heating, as fast cooling encourages the solder to form into a crystalline structure which creates a superior bond to the underlying board. The fourth chamber quickly cools the board, down to temperatures of 86 Degrees Fahrenheit. This process generally takes 30-40 seconds. Timing is crucial here, as the solder must melt fully without having time to flow off the board or start vaporizing. Several heating methods can be used here, although conventional convection baking is still the most common. The heart of the reflow soldering process happens here, where the circuit board is rapidly heated to maximum temperatures to fully melt the solder and bond it to the circuit board. Once the thermal soak is finished and the piece moves on, the board should be at thermal equilibrium. This ensures even heat distribution, as well as activating chemicals in the solder paste that prevent the solder from turning into microbeads, which it otherwise would. Having reached the desired pre-heating point, the board passes to the second chamber for a thermal soak at that temperature, for 60-120 seconds. This stage can last several minutes, as the temperature is only raised by about 3-5 degrees Fahrenheit per second. The heat distribution must be uniform, or the board could warp. The first and lengthiest stage is the pre-heating of the circuit, which requires bringing it up to a given temperature slowly.
#SMD REFLOW OVEN SERIES#
These marvels of engineering can automatically handle the heating and cooling of each circuit board, sending it through a series of internal chambers for treatment. Modern manufacturers utilizing surface mounted technology use all-in-one devices called Reflow Soldering Ovens to ensure proper circuit boards. Much like when cooking dinner, too little or too much heat can quickly ruin the project. While there are several possible techniques, the board has to be precisely raised to temperatures in excess of 200 degrees, to properly melt the solder. The hard part is the baking that follows. Rather than using space-hungry holes through the board, SMT-based circuits have components which are placed directly onto the board, using a solder paste which also works as a glue. Manufacturing based on Surface-Mounted Technology has taken over electrical engineering, and for good reason.
